LEAN Production increases your productivity by at least 20%
LEAN Production is more than short transport routes and tidy tools. It is the consequent implementation to avoid all waste. LEAN Production and Kaizen are buzzwords that we encounter more and more often when it comes to optimizing production processes, reducing waste and achieving continuous improvement. In the future, companies will have to pay more attention to these topics in order to remain competitive. For more than 10 years, we have been optimizing our own production according to LEAN Production principles. Based on our experience and the existing product variety, we are able to offer individual solutions for our customers' needs. Shorter lead times and lower inventories quickly lead to a positive return on investment. Practical experience shows that LEAN Production solutions from Phoenix Mecano can increase productivity by at least 20%.
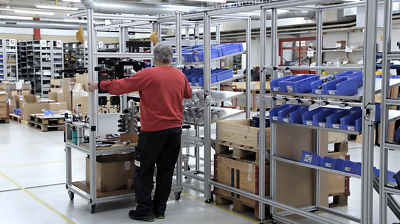
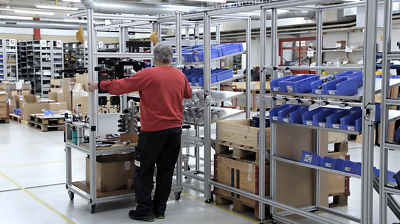